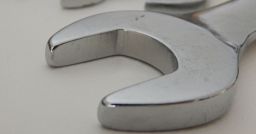
Imparare dagli errori: le scelte pericolose nelle attività di manutenzione
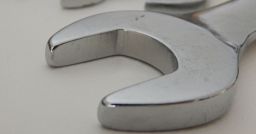
Brescia, 14 Feb – Abbiamo più volte ricordato nei nostri articoli che la manutenzione comprende diverse tipologie di attività, ad esempio di ispezione, collaudo, misurazione, sostituzione, regolazione, riparazione, rilevamento dei guasti, sostituzione dei componenti, assistenza. E molti documenti prodotti dall’Agenzia europea per la sicurezza e la salute sul lavoro (EU-OSHA), durante la campagna europea del 2010/2011 sulla manutenzione sicura, hanno sottolineato che esistono due tipi principali di manutenzione:
- la manutenzione preventiva (proattiva) “eseguita per mantenere qualcosa in condizioni funzionali; generalmente pianificata e programmata conformemente alle istruzioni del produttore;
- la manutenzione correttiva (reattiva) che riguarda la “riparazione di un elemento per renderlo nuovamente funzionante; attività non programmata e non pianificata, generalmente associata a maggiori rischi e pericoli rispetto alla manutenzione preventiva”.
E proprio in relazione ai tanti rischi a cui sono soggetti gli operatori impegnati in attività di manutenzione – che come abbiamo visto sono maggiori nelle attività non programmate e pianificate – torniamo a presentare nella rubrica “ Imparare dagli errori” nuove dinamiche infortunistiche cercando di rimarcarne i fattori causali e di raccogliere utili spunti per la prevenzione.
Gli incidenti presentati sono raccolti nell’archivio di INFOR.MO., strumento per l'analisi qualitativa dei casi di infortunio collegato al sistema di sorveglianza degli infortuni mortali e gravi.
I casi di infortunio e i rischi nella manutenzione
Il primo caso che presentiamo è relativo ad un infortunio durante la manutenzione di una macchina rettificatrice.
Un operaio, con l’aiuto di un collega, ha provveduto a sostituire il piano magnetico di una macchina rettificatrice in quanto quello presente necessitava di interventi di manutenzione. Sul piano nuovo è necessario eseguire alcune passate di rettificatura per rendere la superficie superiore perfettamente ortogonale all’asse verticale della mola.
Dopo aver avviato la mola (operazione necessaria a detta dell’operaio a far cadere sul sottostante piano le impurità costituite da limatura fine, che possono condizionare la qualità della rettificatura) e aver posizionato la stessa in posizione di sicurezza, ovvero il più lontano possibile dalla superficie superiore del piano, l’operaio passa la mano sinistra sul piano al fine di “sentire” al tatto la limatura presente e rimuoverla.
Nell’effettuare tale operazione entra inavvertitamente, con il primo dito della mano sinistra, in contatto con la mola in rotazione riportando una ferita con lesione del tendine estensore.
La scheda indica che il RSPP della Ditta ha “verbalmente dichiarato che l’operazione che ha comportato l’infortunio doveva essere eseguita a macchina spenta, obbligo richiamato anche da idonea cartellonistica esposta nell’officina”.
Questi i fattori causali riportati nella scheda:
- “macchina rettificatrice non a norma”;
- “operazione di pulizia con organi in movimento”.
Il secondo caso riguarda un infortunio avvenuto durante la fase di un intervento di riparazione della zona terminale di una linea di assemblaggio componenti in acciaio, dove si effettuano lavori di taglio e piegatura.
La scheda ricorda che “essendoci presenza di zone di possibili compressioni o schiacciamenti - durante il funzionamento in automatico – tutta la parte terminale della linea è circondata da apposita rete metallica che impedisce l’accesso di eventuali operatori.
Gli accessi in tale zona, per interventi di manutenzione o riparazione, avvengono tramite due porte asservite da micro-interruttori di blocco che impediscono qualsiasi tipo di funzionamento della linea, o di qualsiasi meccanismo collegato ad essa, in caso di apertura delle porte stesse”.
Tuttavia durante un intervento di manutenzione/riparazione, “con accesso alla zona effettuato dalla porta, il braccio dell’infortunato è rimasto schiacciato tra parti mobili. Dalle dichiarazioni dell’infortunato emerge che, al momento dell’infortunio, il micro-interruttore di blocco della porta utilizzata per entrare nella zona di lavorazione era stato artificiosamente escluso. Sempre dalle dichiarazioni dell’infortunato, è stato lui stesso, per velocizzare il lavoro, ad escludere –tramite manomissione - la funzionalità del micro-interruttore applicato sulla porta di entrata. L’infortunato è il capo-reparto e sovrintende al lavoro di circa venti persone”.
E sottolinea la scheda, per ricordare come i comportamenti a rischio possano essere diffusi anche tra il personale più esperto in materia di sicurezza, che l’infortunato era stato nel passato anche “docente-formatore in materia di sicurezza in corsi di formazione per gli addetti al reparto da lui stesso diretto”.
L’approccio strutturato alla manutenzione
Per raccogliere qualche riflessione e qualche spunto utile a migliorare la prevenzione degli infortuni nelle attività di manutenzione possiamo fare riferimento al “ Factsheet 89 - Manutenzione sicura per i datori di lavoro. Lavoratori sicuri - Risparmio di denaro”, un documento correlato alla campagna europea sulla manutenzione sicura.
Nel documento si ricorda che i lavoratori impegnati nelle attività di manutenzione sono esposti a un’ampia gamma di pericoli.
Ad esempio possono “correre il rischio di:
- sviluppare disturbi muscolo-scheletrici (DMS) durante lo svolgimento di attività che comportano posture disagevoli, a volte in condizioni ambientali sfavorevoli (ad esempio al freddo);
- essere esposti all’amianto, durante la manutenzione di vecchi edifici o di installazioni industriali; asfissia in spazi ristretti; esposizione ad agenti chimici (ad esempio grassi, solventi, sostanze corrosive);
- esposizione a rischi biologici: epatite A, legionella;
- esposizione a polveri, comprese polveri di legno cancerogene;
- incidenti (di tutti i tipi, comprese le cadute e gli urti dovuti al distacco di pezzi di macchinari)”.
Il factsheet, rivolto al datore di lavoro, indica che considerata l’ampia gamma di rischi e pericoli associati alla manutenzione “potrebbe essere necessario includerla nel sistema di gestione globale della società”.
E deve essere eseguita “una valutazione approfondita dei rischi, comprendente tutte le fasi dell’attività e tutti i pericoli. Ciò è particolarmente importante per le piccole e medie imprese, perché sono più vulnerabili agli effetti negativi degli incidenti”.
È dunque necessario un approccio strutturato in cui ogni processo di manutenzione “inizia con la fase di progettazione e di pianificazione”. Inoltre è importante:
- “destinare tempo e risorse sufficienti per l’attività di manutenzione”,
- “assicurare la formazione e le competenze del personale addetto alla manutenzione”,
- “istituire sistemi di lavoro sicuri basati su un’adeguata valutazione dei rischi”,
- garantire una “comunicazione efficace tra il personale addetto alla produzione e alla manutenzione”.
Inoltre “una volta portate a termine le operazioni di manutenzione, è necessario eseguire controlli speciali (ispezioni e test) per assicurare che la manutenzione sia stata eseguita correttamente e che le apparecchiature o il luogo di lavoro vengano lasciati in condizioni sicure per il proseguimento delle operazioni”.
Riguardo, in particolare, ai sistemi di lavoro si indica che la manutenzione “può comportare l’arresto di un processo di produzione e può richiedere che gli addetti operino in posizioni insolite e pericolose (ad esempio all’interno di un macchinario o impianto)”.
Il problema è che, come abbiamo visto riguardo ad uno dei due incidenti presentati, che la manutenzione “viene eseguita spesso sotto pressione: per riavviare un processo di produzione interrotto, o ultimare i lavori programmati prima di una scadenza. Gli addetti alla manutenzione potrebbero anche dovere lavorare con macchinari che non dispongono delle abituali misure di sicurezza”.
Di conseguenza è necessario che venga istituito “un sistema, basato sulla valutazione dei rischi, per garantire che la manutenzione possa essere eseguita in maniera sicura, che i lavoratori impegnati in un processo di produzione continuo rimangano sicuri e che l’apparecchiatura possa essere avviata in seguito in maniera sicura. Dovrebbe essere acclusa all’abituale documentazione sull’attività, un documento sulla valutazione dei rischi”.
Rimandiamo alla lettura integrale del factsheet che riporta ulteriori indicazioni e suggerimenti per i datori di lavoro riguardo a:
- formazione e competenze del personale addetto alla manutenzione,
- disponibilità delle apparecchiature e dispositivi necessari per aumentare la sicurezza,
- criticità nei subappalti,
- manutenzione intesa come processo.
Tiziano Menduto
Sito web di INFOR.MO.: nell’articolo abbiamo presentato le schede numero 5994 e 5959 (archivio incidenti 2002/2015).

I contenuti presenti sul sito PuntoSicuro non possono essere utilizzati al fine di addestrare sistemi di intelligenza artificiale.
Pubblica un commento
Rispondi Autore: Andrea Decorato ![]() | 14/02/2019 (08:20:47) |
Buongiorno Redazione, per quanto riguarda il primo caso bisognerebbe controllare se la macchina rettificatrice avesse già una segnaletica di informazione e di divieto.Inoltre il D.Lgs (Art. 74) prevede già una segnaletica obbligatoria da apporre sul luogo di lavoro. Molto spesso non viene letta o considerata. Nel secondo caso, invece, non penso che sia la prima volta che venga escluso l'interruttore per la manutenzione. La sicurezza "Fai da te" non porta a niente. Informazione, formazione ed addestramento devono essere pubblicizzati sempre come l'uscita di uno smartphone nuovo! Distinti saluti. |