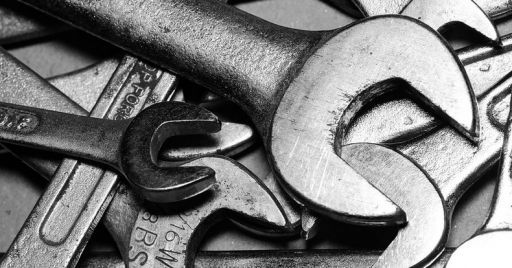
Quali sono i rischi associati alle attività di manutenzione?
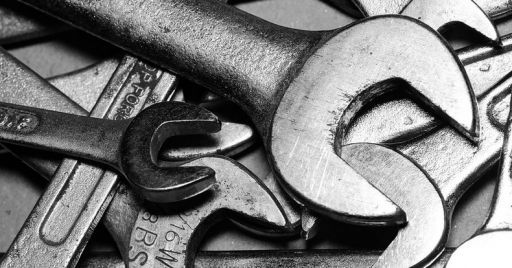
Monza, 10 Nov – Come ricordato nei nostri articoli, la manutenzione, svolta regolarmente, è un elemento fondamentale per mantenere efficienza e sicurezza di attrezzature e macchinari nel tempo. Negli ambienti di lavoro, come sottolinea la campagna europea 2010/2011 sulla manutenzione sicura, sono infatti molti gli incidenti mortali sul lavoro che sono collegati a carenze della manutenzione.
Tuttavia, secondo anche quanto visto anche nella rubrica “ Imparare dagli errori”, non sono pochi anche gli infortuni negli interventi manutentivi. E dunque la manutenzione deve essere considerata un’attività ad alto rischio e “deve essere eseguita in modo sicuro, con un’adeguata protezione, sia per gli addetti alla manutenzione che per le altre persone eventualmente presenti sul posto di lavoro”.
A ricordare i rischi delle attività di manutenzione è il documento “ Utilizzo in sicurezza delle macchine. Guida per le imprese” prodotto dall’ ATS Brianza ed elaborato attraverso il lavoro del gruppo “Sicurezza macchine” costituito nell’ambito del Comitato di Coordinamento Provinciale di Monza e Lecco ex art.7 D.Lgs. 81/08.
Nel documento un capitolo si sofferma sul mantenimento nel tempo della sicurezza delle macchine ed impianti e, oltre a fornire informazioni su cosa sia la manutenzione ordinaria e straordinaria, riporta utili considerazioni e indicazioni sui rischi associati alle attività di manutenzione.
Ci soffermiamo oggi sui seguenti argomenti:
- I rischi specifici nelle attività di manutenzione
- La manutenzione e la valutazione dei rischi
- Le misure di prevenzione e il riavvio dei macchinari
I rischi specifici nelle attività di manutenzione
Il documento sottolinea che oltre ai normali rischi associati a qualsiasi ambiente di lavoro, “durante le operazioni di manutenzione i lavoratori sono esposti ad alcuni rischi specifici. Ad esempio, nella manutenzione di un macchinario che fa parte di una linea di produzione, può essere necessario, durante l’esecuzione di un processo, di dover operare in prossimità di organi in movimento o di elementi attivi in tensione”.
In particolare durante il normale funzionamento dei macchinari “sono i dispositivi di sicurezza che riducono la probabilità di un errore umano che possa portare a incidenti, mentre nelle condizioni in cui si trovano ad operare i lavoratori che eseguono la manutenzione, la probabilità che possa aversi un contatto diretto tra il lavoratore e gli organi in movimento o le parti sotto tensione è più alta. Per questo motivo, è opportuno che siano individuati i limiti di azione di ogni lavoratore prevedendo almeno un soggetto preposto alla manutenzione delle macchine/impianti che sia in possesso di adeguate competenze”.
Ricordando che in allegato al documento è presente una descrizione delle mansioni e delle competenze di un manutentore, la guida dell’ATS segnala poi che:
- la manutenzione spesso “comporta un lavoro insolito o attività non di routine ed è spesso eseguita in condizioni eccezionali, ad esempio lavorando in spazi ristretti;
- le operazioni di manutenzione potrebbero riguardare lo smontaggio e il rimontaggio di attrezzature complesse: in situazioni simili il rischio di errore umano cresce e aumenta il pericolo di incidenti”;
- “in caso di appalti per l’esecuzione di lavori di manutenzione, i lavoratori inviati ad eseguire interventi presso le società appaltanti si trovano spesso a dover cambiare contesto lavorativo e ambiente, e ciò ha come risultato un incremento del rischio di commettere errori che possano dar luogo ad incidenti. Gli appalti multipli e i subappalti sono fattori aggravanti in termini di sicurezza e salute; infatti numerosi incidenti riguardano attività di manutenzione in appalto multiplo o subappalto”;
- “in alcune realtà produttive i tempi per l’esecuzione della manutenzione devono essere necessariamente ridotti, in particolare quando sono coinvolti rallentamenti o arresti della produzione: in casi simili, le riparazioni ed il ripristino della produzione divengono attività ad alta priorità, ed i lavoratori si trovano a dover operare sotto la pressione del tempo”.
La manutenzione e la valutazione dei rischi
La guida ricorda poi che il D.Lgs. 81/2008 “impone a tutte le imprese di condurre la valutazione di tutti i rischi compresi quelli derivanti dalle attività di manutenzione”.
La valutazione del rischio per le operazioni di manutenzione – continua il documento – “è un compito particolarmente difficile a causa delle incertezze del lavoro manutentivo; è possibile, infatti, dover iniziare un certo intervento di manutenzione correttiva e scoprire che ulteriori interventi non previsti sono necessari. Per tale motivo è opportuno coinvolgere nel processo di valutazione del rischio gli stessi lavoratori che effettuano le attività manutentive”.
Infatti “senza il contributo di coloro che eseguono il lavoro, è difficile identificare tutti i pericoli, analizzare i vari aspetti del lavoro e le situazioni che potrebbero sorgere e decidere i metodi più efficaci e adeguati per prevenire e controllare il rischio”.
Inoltre sarebbe utile fornire, per ogni intervento manutentivo che debba essere effettuato, “un’apposita scheda che fornisca al lavoratore una panoramica dei risultati della valutazione del rischio per quel determinato lavoro e riassuma tutti i rischi che potrebbero essere presenti”.
Le misure di prevenzione e il riavvio dei macchinari
Chiaramente di estrema importanza risultano poi essere “l’individuazione e l’applicazione delle misure di prevenzione riguardanti le attività di manutenzione macchine/impianti assegnate alle varie figure aziendali”.
In particolare tra i principali accorgimenti, in fase di manutenzione, “risulta necessario la corretta gestione delle chiavi a bordo macchina” (se ne parla nell’Allegato M “Gestione delle chiavi a bordo macchina”).
Segnalando che “una delle principali cause di incidente ed infortunio nelle fasi di manutenzione o pulizia di una macchina o di un impianto è la riattivazione non intenzionale o inattesa di fonti di energia”, si indica che per proteggere i lavoratori dalle sorgenti di energia pericolose durante tali operazioni, si è dimostrata efficace una procedura elaborata dalla OSHA (standard 29 CFR 1910.147), rispondente anche a quanto previsto dall’Allegato V del D.Lgs 81/2008 (Punto 11, parte I, “Manutenzione, riparazione, regolazione, ecc”).
La procedura, nota come lockout/tagout (LOTO), “fissa i criteri e le prassi lavorative da attuare per:
- identificare le fonti di energia pericolose;
- isolare e/o dissipare tali energie;
- procedere alla fermata ed al riavvio di un macchinario in sicurezza”.
Concludiamo segnalando che nell’Allegato N (Introduzione alla procedura di lockout/tagout) della guida si riportano alcune indicazioni specifiche per adottare tale procedura. Un altro allegato (Allegato O) riporta, invece, un facsimile della “Procedura di controllo e manutenzione macchine”.
Scarica il documento da cui è tratto l'articolo:

I contenuti presenti sul sito PuntoSicuro non possono essere utilizzati al fine di addestrare sistemi di intelligenza artificiale.