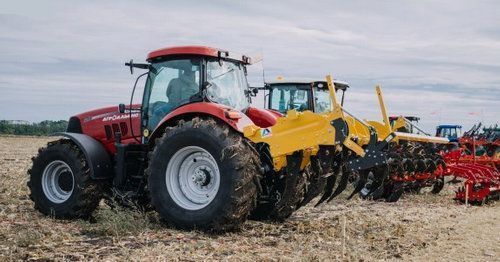
Macchine agricole: come ridurre l’esposizione a rumore e vibrazioni?
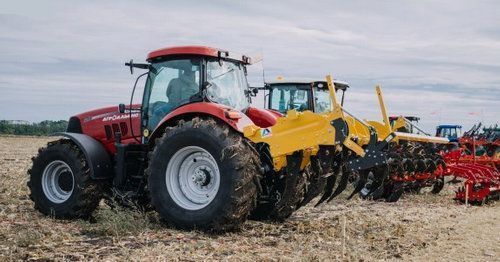
Roma, 11 Nov – Agli agenti fisici rumore e vibrazioni, come ricordato anche nei nostri articoli, sono esposti in modo particolare alcuni lavoratori, ad esempio gli operatori delle macchine agricole, con ripercussioni significative in termini di comfort e sicurezza. Ripercussioni che possono avere diverse conseguenze sullo stato della salute: compromissione della funzione uditiva, problemi di natura vascolare e osteoarticolari, lesioni del tratto lombare o trauma del rachide, ….
Con riferimento ai suddetti operatori e con l’intento di favorire una progettazione efficace in grado di ridurre il rischio vibrazione e il rischio rumore per i mezzi agricoli, nei mesi scorsi abbiamo presentato il documento “ Progettazione acustica e vibratoria di macchine e attrezzature per uso agricolo. Manuale operativo” prodotto dal Dipartimento di medicina, epidemiologia, igiene del lavoro e ambientale (DIMEILA) dell’ Inail.
Nella presentazione del documento abbiamo affrontato in particolare le possibili conseguenze dell’esposizione ai due agenti fisici, cominciando ad accennare anche a possibili suggerimenti operativi per la prevenzione (ad esempio con riferimento alla riduzione delle vibrazioni nei trattori).
Oggi, sempre con riferimento al contenuto del documento Inail, ci soffermiamo sui principi generali relativi alla trasmissione ed isolamento delle vibrazioni e del rumore con particolare attenzione ai seguenti argomenti:
- Rischio vibrazione: l’importanza di una progettazione accurata
- Rischio vibrazione: l’inserimento di sistemi antivibranti
- Rischio rumore: gli interventi per le sorgenti di rumore
Rischio vibrazione: l’importanza di una progettazione accurata
Riguardo alle vibrazioni il manuale - a cura di Annalisa Fregolent, Pietro Nataletti, Walter D’Ambrogio e Jacopo Brunetti – ricorda che secondo la Direttiva macchine (d.lgs.17/2010), ‘La macchina deve essere progettata e costruita in modo tale che i rischi dovuti alle vibrazioni trasmesse dalla macchina siano ridotti al livello minimo, tenuto conto del progresso tecnico e della disponibilità di mezzi atti a ridurre le vibrazioni, in particolare alla fonte’.
Infatti le macchine “trasmettono vibrazioni meccaniche alle strutture a cui sono collegate e di conseguenza anche ai lavoratori che operano in contatto con queste strutture. Ad esempio, in una macchina agricola ci sono numerose sorgenti di vibrazioni che possono essere trasmesse al conducente attraverso il sedile”.
È dunque necessario valutare l’esposizione del lavoratore a tali vibrazioni ed “intervenire laddove questa esposizione possa procurare effetti dannosi sulla salute”. E per una “effettiva riduzione dell’esposizione dell’operatore a vibrazioni eccessive, è necessaria una progettazione accurata che tenga conto degli aspetti vibrazionali”.
Ad esempio - come indicato nella UNI CEN/TR 15172-1 (Vibrazioni al corpo intero - Linee guida per la riduzione del rischio da vibrazione - Parte 1: Metodo tecnico progettuale per la progettazione delle macchine) - è necessario: “identificare le sorgenti principali di vibrazioni; ridurre l’ampiezza delle vibrazioni alla sorgente; ridurre la trasmissione delle vibrazioni dalla sorgente all’operatore”.
In particolare, dopo aver “preliminarmente individuato e caratterizzato le sorgenti e le vie di trasmissione, possono essere necessari degli interventi locali per ridurre la risposta vibratoria di particolari elementi della macchina (ad es. le vibrazioni sul sedile dell’operatore), al fine di rispettare i requisiti imposti dalla legge”.
Gli autori segnalano che la “modifiche strutturali” rappresentano un possibile approccio a tale problema, “in quanto sono una procedura che ha lo scopo di identificare le modifiche più efficaci da apportare ad un sistema vibrante affinché questo abbia il comportamento dinamico desiderato”. E nell’ambito delle modifiche strutturali “si possono distinguere due tipi di problemi:
- il problema diretto consiste nella valutazione dell’effetto di cambiamenti già definiti per la verifica dell’efficacia delle modifiche adottate sul comportamento dinamico del sistema;
- il problema inverso permette di identificare nell’ambito di un certo insieme di possibili modifiche, quelle da apportare per ottenere il comportamento dinamico desiderato.
Entrambi gli approcci possono essere adottati sia in fase di progettazione di nuove macchine che in fase di bonifica delle macchine esistenti”.
Rischio vibrazione: l’inserimento di sistemi antivibranti
Si segnala poi che tra le possibili modifiche apportabili al sistema c’è “l’inserimento di sistemi antivibranti” e gli autori, “data l’importanza che rivestono nella pratica della progettazione vibrazionale di sistemi meccanici”, analizzano i principi di funzionamento.
Il documento, prima di procedere ad una descrizione dei vari sistemi, fornisce una classificazione “in base a:
- Principio di funzionamento:
- sistemi passivi: introducono una modifica nel sistema meccanico in termini di caratteristiche di massa, smorzamento o rigidezza; non sono sistemi del tutto in grado di adattarsi alla variazione delle eccitazioni esterne, alle variazioni delle condizioni di funzionamento o alle variazioni delle proprietà dinamiche del sistema;
- sistemi attivi: sono caratterizzati dalla presenza di un sistema di attuazione che introduce una sorgente di eccitazione aggiuntiva finalizzata al controllo delle vibrazioni;
- sistemi semi-attivi: analogamente ai sistemi passivi introducono una modifica nel sistema meccanico ma sono capaci di adattarsi alle variazioni delle eccitazioni esterne, alle variazioni delle condizioni di funzionamento e alle variazioni delle proprietà dinamiche del sistema stesso.
- Posizionamento nel sistema:
- all’interfaccia tra due strutture: ha la funzione di isolare una struttura dall’altra;
- all’interno della struttura: ha la funzione di controllare le vibrazioni nel punto in cui vi sono particolari requisiti in termini di livelli di vibrazione;
- alla sorgente: ha la funzione di ridurre le eccitazioni che causano le vibrazioni.
Una tabella riporta schematicamente la classificazione dei sistemi antivibranti in base al posizionamento e al principio di funzionamento:
Rischio rumore: gli interventi per le sorgenti di rumore
Veniamo poi al rischio rumore.
Si indica che le macchine “devono essere progettate e costruite in modo da ridurre al minimo i rischi risultanti dall’esposizione dei lavoratori al rumore prodotto dalla macchina”.
Infatti nelle macchine sono “presenti delle sorgenti di vibrazione che possono:
- generare, attraverso il processo di irradiazione acustica, rumore che mette in vibrazione altre parti della macchina o raggiunge direttamente l’operatore (via di trasmissione aerea), oppure
- trasmettere per via strutturale tali vibrazioni ad altre parti della macchina (via di trasmissione strutturale), le quali a loro volta possono irradiare rumore”.
Il documento, che, ricordiamolo ancora, si occupa di macchine e attrezzature per uso agricolo, segnala che, ad esempio, “in una macchina agricola ci sono numerose sorgenti di vibrazione che possono:
- irradiare rumore che mette in vibrazione le pareti della cabina del trattore e che da queste viene irradiato all’interno, oppure raggiunge direttamente l’operatore;
- trasmettersi per via strutturale alle pareti della cabina, che irradiano rumore all’interno della cabina stessa”.
Si indica poi che altre fonti di rumore possono derivare “da risonanze acustiche nei condotti (rumore emesso da macchine operatrici pneumatiche) o da fenomeni aero-acustici (getti turbolenti)”.
È dunque necessario valutare l’esposizione del lavoratore al rumore e intervenire “laddove questa esposizione possa procurare effetti dannosi per la salute”.
Anche nel caso della riduzione dell’esposizione dell’operatore a rumore eccessivo, è importante una “progettazione accurata che tenga conto degli aspetti vibrazionali già trattati”, sia pure in “un campo di frequenze più ampio, e del modo in cui tali vibrazioni vengono convertite in rumore”.
Ed è necessaria “una analisi per localizzare le principali sorgenti di rumore, le vie di trasmissione e le superfici irradianti e identificare quelle che danno il contributo maggiore. Infatti, per ottenere una significativa riduzione del rumore è necessario partire dall’attenuazione delle sorgenti con maggiore emissione, in quanto l’eliminazione delle sorgenti minori può non avere alcun effetto sulla diminuzione del rumore complessivo”.
Inoltre per ridurre il livello di rumore al quale è sottoposto l’operatore, “possono essere necessari degli interventi locali e mirati come ad esempio l’introduzione di silent-block per limitare la trasmissibilità per via strutturale di vibrazioni a frequenze medio alte in grado di eccitare strutture, o pannelli capaci di irradiare rumore (ad esempio, tra telaio del trattore e cabina)”. E in relazione al problema di controllo da affrontare – “riduzione del rumore trasmesso in un ambiente contiguo o riduzione del rumore all’interno dell’ambiente in cui è presente la sorgente” – “si possono distinguere due categorie di materiali:
- materiali fonoisolanti (opachi o trasparenti) per abbattere il livello del rumore trasmesso dall’esterno all’interno di un ambiente confinato attraverso le sue pareti (ad esempio, la cabina di un trattore). Le prestazioni di un materiale fonoisolante sono generalmente indicate per mezzo dell’indice di riduzione sonora, altrimenti noto come perdita di trasmissione: dove indica il coefficiente di trasmissione sonora, o trasmissibilità, dato dal rapporto tra l’intensità del suono trasmesso e quella del suono incidente su un pannello;
- materiali fonoassorbenti per abbattere il livello del rumore presente all’interno di un ambiente confinato (ad esempio, all’interno della cabina di un trattore). L’energia sonora viene assorbita, cioè convertita in calore per attrito all’interno di materiali porosi o fibrosi. I materiali porosi, come quelli in fibra di vetro, lana di roccia e schiuma plastica porosa, devono essere sufficientemente ‘aperti’ da consentire all’onda sonora di entrare nei canali contenenti aria, ma sufficientemente ‘chiusi’ da presentare una notevole resistenza al moto ondoso nei suddetti canali. La capacità fonoassorbente di un materiale poroso o fibroso è definita per mezzo del coefficiente di assorbimento dato dal rapporto tra l’intensità sonora assorbita dalla superficie e quella incidente”.
Chiaramente se gli interventi illustrati non fossero attuabili o sufficienti - concludono gli autori - “si può optare per l’adozione di dispositivi di protezione individuale (DPI), quali tappi, caschi, cuffie a controllo passivo e attivo”.
Segnaliamo, in conclusione, che riguardo alle possibili soluzioni per la trasmissione ed isolamento delle vibrazioni nelle macchine e attrezzature per uso agricolo, come indicato in precedenza, il documento si sofferma in particolare su:
- sospensioni passive
- sospensioni semi-attive
- sospensioni attive
- assorbitori dinamici passivi
- assorbitori semi-attivi
- assorbitori attivi
- risonatori passivi, semi-attivi e attivi.
RTM
Scarica il documento da cui è tratto l'articolo:
Inail, Dipartimento di medicina, epidemiologia, igiene del lavoro e ambientale, “ Progettazione acustica e vibratoria di macchine e attrezzature per uso agricolo. Manuale operativo”, a cura di Annalisa Fregolent (Università degli Studi di Roma La Sapienza - Dipartimento di ingegneria meccanica e aerospaziale), Pietro Nataletti (Inail – Dimeila), Walter D’Ambrogio e Jacopo Brunetti (Università degli Studi dell’Aquila - Dipartimento di ingegneria industriale e dell’informazione e di economia), manuale predisposto nell’ambito del progetto Bric Inail ID26 del Piano delle attività di ricerca Inail 2016 - 2018, Collana Salute e Sicurezza, edizione 2021 (formato PDF, 4.09 MB).
Vai all’area riservata agli abbonati dedicata a “ Informazioni su progettazione acustica e vibratoria di macchine e attrezzature per uso agricolo”.

I contenuti presenti sul sito PuntoSicuro non possono essere utilizzati al fine di addestrare sistemi di intelligenza artificiale.